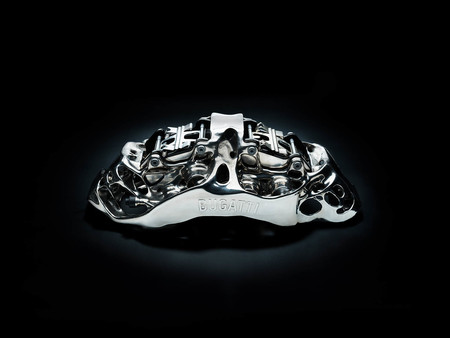
Bugatti, al igual que muchos otros fabricantes, como Koenigsegg en el One:1, investiga la impresión de piezas en 3D. Para los ingenieros, la impresión 3D es como la respuesta a todas sus plegarias a la hora de crear un prototipo en poco tiempo (adiós a los moldes, a la fundición, etc). De este modo se puede ver, probar y tocar un nuevo producto con un coste ínfimo comparado con el método habitual de fabricación.
En el caso de Bugatti, la marca de Molsheim, imprimió lo que viene siendo la pinza de freno en titanio más grande del mundo. Se trata de un pinza de 8 pistones destinada al eje delantero del Bugatti Chiron que mide 40 cm de largo y pesa 2,9 kg. Es una pieza 40 % más ligera que las actuales pinzas de frenos que equipa el Chiron.
El Bugatti Chiron equipa normalmente pistones de frenos de aleación de aluminio, con ocho pistones delante y seis en las pinzas traseras. Para la pinza de freno de titanio, Bugatti utilizó titanio normalmente empleado en la industria aeronáutica y aeroespacial. Bugatti asegura que se puede aplicar una fuerza de 125 kg por mm cuadrado sobre ese titanio sin que el material se rompa.
Una impresión 3D tan larga como la fabricación del Bugatti Chiron
La impresión se realizó en 45 horas en una impresora 3D equipada con cuatro láser de 400 vatios y fueron precisas 2.213 capas de titanio. Los láser derretían la capa de polvo de titanio en la forma deseada para obtener la pinza de freno. La pinza uina vez impresa necesita un tratamiento térmico (horno a 700º C que baja progresivamente hasta los 100º C), mientras que los acabados se hacen con procesos químicos y físicos.
De momento, los Chiron seguirán saliendo de la factoría de Molsheim (donde cada equipo de 20 personas tarda seis meses en completar un coche) con las pinzas de freno de aleación, pero la marca comienza estos días las pruebas con estas nuevas pinzas antes de integrarlas al proceso de fabricación de las siguientes unidades del Chiron hacia el final del año.