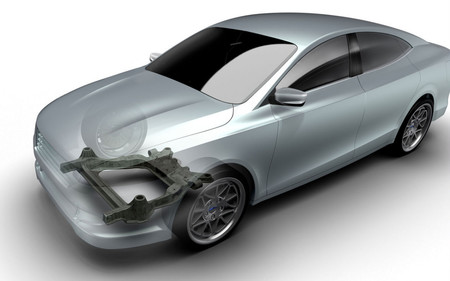
Fruto de la colaboración en investigación y desarrollo entre Ford Motor Company y el especialista Magna, este prototipo de subchasis fabricado en fibra de carbono supone un gran avance con respecto a los convencionales de acero. Además de ser más sencillo, con un 87% menos de componentes, este subchasis es también una tercera parte más ligero, concretamente un 34%.
Por el momento, varios vehículos de pruebas están haciendo ya kilómetros con este subchasis recién desarrollado, aún un prototipo, que está formado por dos secciones de polímero reforzado con fibra de carbono (CFRP) unidas mediante remaches estructurales y adhesivo, y sólo cuatro componentes metálicos, frente a las 45 diferentes piezas de un subchasis al uso.
La importancia de este avance es que el subchasis de un automóvil, normalmente de aceros estampados, es una pieza clave en la estructura del vehículo ya que normalmente es el lugar donde se fija el motor y otros componentes del eje delantero, y que además ha de contribuir a la rigidez del conjunto y tener las cualidades necesarias para soportar impactos frontales.
Esta creación, que ahora se prueba en vehículos Ford, es principalmente obra del equipo de ingenieros y diseñadores de Magna, y ha pasado todas las pruebas 'virtuales' de resistencia, pero hora tendrá que enfrentarse a otros retos como la evaluación de posibles daños por corrosión o por golpes de piedras (por ejemplo). ¿Y la principal ventaja? Pues el ahorro de peso, que conlleva también un ahorro de combustible para el usuario y unas emisiones contaminantes inferiores.
"Hemos sidos pioneros en el uso de materiales ligeros desde hace muchos años. Primero lanzamos el capó de fibra de carbono para los Cadillac CTS-V y ATS-V, y después un refuerzo de carbono para la parrilla del Mustang Shelby Cobra GT 500. Aplicar nuestra experiencia a un componente estructural como el subchasis es un paso adelante para seguir ayudando a que las compañías que trabajan con nosotros alcancen sus metas", concluye Grahame Burrow, presidente de Magna Exteriors.