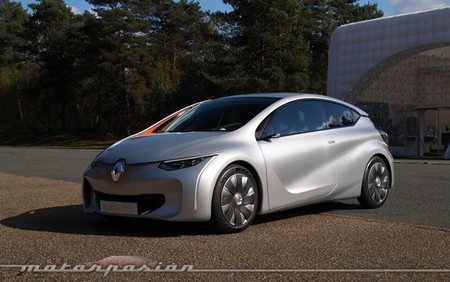
Así es el Renault Eolab (parte 1)
En el Salón del automóvil de París pudimos ver el concept car del Renalt Eolab, el prototipo de utilitario híbrido enchufable de Renault, que homologa un consumo combinado de 1,0 l/100 km de gasolina. Se diferencia de la unidad que se ha construido, principalmente por ser un poco más llamativo, recurriendo a una apertura total de las puertas sin pilar B (el montante central), y a un interior más conceptual y onírico, además de otros pequeños detalles.
Sin embargo el Renault Eolab que hemos ido a conocer al circuito CERAM en Mortefontaine, al noreste de París, en mitad de un precioso bosque, es la única unidad pensada para rodar, conducir y probar en todo tipo de circunstancias, para comprobar en la realidad qué tal funcionan las soluciones técnicas planteadas.
Renault Eolab: el híbrido enchufable francés de 1,0 l/100 km
El Renault Eolab es un utilitario de segmento B de 4,07 m de largo y 1,73 m de ancho. Es muy parecido a un Renault Clio IV (2012), pero más bajo. De hecho el objetivo era hacer una especie de Clio IV, de similar tamaño, con el mismo espacio, habitabilidad, maletero, comodidad y prestaciones, pero que aplicando múltiples soluciones desde cero, consumiera lo mínimo posible.
Así se han aplicado 100 medidas diferentes, englobadas en tres grandes materias: aerodinámica, peso y motorización. Consiguen finalmente un consumo combinado homologado de tan solo 1,0 l/100 km (Europa) de gasolina. Estamos hablando de un coche híbrido enchufable con una autonomía en modo exclusivamente eléctrico de 60 km.
Es inevitable compararlo con el Volkswagen XL1, que también recurre a una mejor aerodinámica, menor peso y motorización híbrida enchufable, aunque en este caso diésel, para tener un consumo combinado homologado de tan solo 0,9 l/100 km.
Hay dos diferencias importantes entre ambos. La primera es que el XL1 solo tiene dos plazas y un maletero pequeño, mientras que el Eolab tiene cinco y un maletero similar al de un Clio. La segunda es el precio, el alemán cuesta unos 110.000 euros, pero el francés sería asequible y costaría solo un poco más caro que un coche equivalente de gasolina y cambio automático, según nos contó Renault (que tampoco precisó más). El objetivo no es tener un coche que sorprenda por su consumo, sino que además de eso pueda ser comprado por cuanta más gente mejor.
Hay que dejar claro que el Renault Eolab solo es un prototipo y un escaparate de demostración, experimentación y prueba de tecnologías. No va a pasar a producción. Eso sí, casi todas las medidas que se han aplicado en él se irán implantando en los modelos de serie poco a poco, desde ahora hasta el año 2020, para ir reduciendo consumos, sin que se note una subida de su precio por ello.
Sí confirma Renault que para 2017 o 2018 podría poner a la venta un coche híbrido enchufable, pero sin embargo dice que no sabe muy bien en qué segmento. No tiene por qué ser un Clio futuro, ni un modelo que se parezca al Eolab, podría ser eso, o podría ser un nuevo Megane o un nuevo Laguna, ya se verá. Pero habrá un híbrido enchufable, eso sin duda.
Es importante entender también, y nos quedó claro después de probar el coche en circuito, que hay cosas que mejorar (os los comentamos más detalladamente en la segunda parte). Esta unidad la podríamos denominar alfa, haciendo el símil con los programas informáticos, pues todavía se está trabajando en algunos aspectos y componentes que aún hay que mejorar. Esto llevará varios años, de cara a tener un producto redondo y perfecto de cara a ponerlo a la venta.
Un 30% menos de resistencia aerodinámica
La primera gran área de trabajo ha sido la aerodinámica. ¿Es esto algo nuevo? Realmente no, como reconocía el ingeniero responsable de esta parte. Desde hace décadas es bien sabido que a mejor aerodinámica, menor es el consumo, sobre todo a partir de cierta velocidad.
Lo que se ha intentando es aunar una aerodinámica sobresaliente con un diseño exterior que siga siendo agradable y atractivo. Se han tomado medidas tanto en aerodinámica pasiva, es decir, la que está en el propio diseño y forma de la carrocería, como en aerodinámica activa, es decir de elementos que se modifican dinámicamente dependiendo de la velocidad.
En la aerodinámica pasiva tenemos:
El coche es más bajo que un Clio IV equivalente y el morro también lo es. La zaga se ha alargado y bajado el techo en forma de gota de agua, la parte posterior es más estrecha que la parte delantera y el techo a su vez también es todavía más estrecho.
Se incluyen varios elementos de mejora aerodinámica como el alerón posterior, los pilotos, el difusor inferior integrado en el paragolpes, el suelo carenado, y hay además canalizadores del flujo de aire, a ambos lados del paragolpes y en ambos pilares A (cortinas de aire), que reducen turbulencias.
Los neumáticos más estrechos y altos desarrollados por Michelin, las cámaras retrovisoras en lugar de espejos tradicionales, y los tiradores de las puertas enrasados con la carrocería, ofrecen también menos resistencia aerodinámica.
En la aerodinámica activa tenemos:
La altura del coche es variable, mediante una suspensión neumática, y se hace de manera automática dependiendo de la velocidad: a más velocidad el coche baja.
El alerón delantero inferior es replegable, a más velocidad se despliega y baja, para reducir el paso de aire por debajo del coche y pegar un poco más el morro al suelo.
Las llantas de aleación tienen una cubierta dinámica que cierra las aberturas a alta velocidad o bien las abre a baja velocidad o si se nota un sobrecalentamiento de los frenos.
En la parte posterior, a ambos lados del paragolpes, casi en la esquina, detrás de las ruedas, hay sendos flaps que se despliegan hacia fuera a alta velocidad y reducen las turbulencias posteriores.
Cuando el coche está parado la altura al suelo es máxima, para que sea más cómodo y fácil subir y bajarse (sin tener que tirarse). Al empezar a circular la carrocería desciende 25 mm, y al acelerar y sobrepasar los 70 km/h la carrocería vuelve a descender otros 25 mmm, como hemos dicho antes, automáticamente.
Con todas estas estrategias se ha reducido la superficie frontal a 2,0 metros cuadrados y se tiene un coeficiente de resistencia Cx de 0,235, con lo que resulta un SCx de 0,470 metros cuadrados, aproximadamente un 30% menos que en un Renault Clio IV. Esto significa por ejemplo que a velocidad constante de 130 km/h se ahorra del orden de 1,2 l/100 km de gasolina.
400 kg menos de peso sin complicados procesos productivos
Otro aspecto fundamental para el consumo es el peso del coche, o exactamente la masa. Con respecto a un Clio IV, a igualdad de motor, se ha reducido el peso del Renault Eolab en 400 kg. Esto se ha conseguido reduciendo:
130 kg en la carrocería.
160 kg en el chasis y cadena de tracción.
110 kg en el interior, revestimientos, equipamiento y otros elementos.
Un Renault Clio IV pesa 1210 kg, pero el Renault Eolab pesa 955 kg. No son 400 kg menos directamente debido a los 145 kg que "engorda" debido al sistema híbrido, que implica dos motores, térmico y eléctrico, y no uno solo, y una batería que aunque es pequeña, pesa bastante.
Se tuvo en cuenta la reducción de consumo que aporta el sistema híbrido frente al peso que añade, y se comprobó que sale muy a cuenta. Con el motor de gasolina TCe de 120 CV del Clio, el Eolab, que pesaría unos 810 kg, consumiría unos 3,2 l/100 km de gasolina, pero con el sistema híbrido, que da algún caballo más hablando de potencia combinada, pero rinde la misma aceleración, se consigue tener ese consumo de 1,0 l/100 km.
Tal y como nos explicó el ingeniero responsable de los materiales, aligeramiento y construcción del coche, era muy importante contener el precio final del coche para que siguiera siendo asequible, y para ello han buscado materiales cuyos procesos de fabricación fueran sencillos y ya estuvieran implementados en las factorías de Renault, o fueran fácilmente implantables sin grandes costes.
Puzle de materiales
El Renault Eolab es una especie de puzle con piezas hechas cada una del material más adecuado para su función y nivel de resistencia.
Así en algunas partes, normalmente el frontal, los pilares A y los largueros, que deben resistir impactos frontales y garantizar la indeformabilidad del habitáculo, se han empleado aceros de ultra alta resistencia (TTHLE), ahora mismo los de mayor índice elástico que se fabrican, de entre 1200 y 1500 Mpa. Al ser más resistente se requiere menos sección en las piezas y eso ahorra peso. Para dar forma a las piezas se debe recurrir al conformado en caliente
En otras partes se ha utilizado aluminio, ya sea en chapa embutida, en caliente o en templado, ya sea en forma de perfil extrusionado o en fundición. En componentes con mayor solicitación se recurre a aleaciones de aluminio más resistentes y a la fundición en una sola pieza. Por ejemplo las puertas y aletas posteriores son de este material o la barra que está detrás del salpicadero.
Hay otras partes del coche que se realizan en polímero reforzado con fibras largas de vidrio, por ejemplo el montante del pilar B derecho, el suelo de la plataforma del coche o el respaldo de los asientos posteriores. También se utiliza plástico inyectado reforzado con fibra de vidrio en componentes de la carrocería como el capó del motor, las puertas delanteras o el portón del maletero.
Y finalmente, en menor cantidad, también se utiliza el magnesio, un metal todavía más ligero que el aluminio. Por ejemplo el techo es de chapa embutida en templado de magnesio, lo cual es toda una novedad, y la estructura de la puerta derecha es de fundición de magnesio. El techo pesa tan solo 4,5 kg (cuando uno normal de acero pesaría como 10,5 kg). Hay que tener en cuenta que no se emplea el magnesio "puro" sino aleado con un poco de aluminio y zinc. El proveedor Posco se ha encargado del magnesio y del acero.
El inconveniente del magnesio es que se oxida con facilidad. Para evitarlo se tiene especial cuidado en dos aspectos: que la pieza esté perfectamente pintada con varias capas, y la segunda que no haya un contacto directo entre la pieza de magnesio y la de acero.
Pensemos que la densidad del acero viene a ser de unos 7850 kg por metro cúbrico, mientras que la del aluminio es de unos 2700 kg y la del magnesio unos 1740 kg. Nótese lo ligerísimo que es el magnesio en comparación con el acero.
Otra cuestión importante era pensar en las uniones de diferentes piezas de diferentes materiales, no pudiendo recurrir en todas partes a la soldadura, como se puede hacer con una carrocería íntegramente de acero.
Así que según la pieza y los materiales se recurre a la soldadura, pero también a uniones mecánicas, con tornillos o remaches (por ejemplo entre piezas de fibra de vidrio y acero) o a uniones químicas, con adhesivos (se utiliza un pegamento de altas prestaciones para pegar el techo de magnesio a la estructura de acero).
Cualquier pieza puede pesar menos
Además de todo esto práticamente todos los componentes o piezas del coche se han aligerado: tren de rodaje más ligero, dirección más ligera, sistema de frenos más pequeño y ligero, neumáticos más ligeros, vidrios más ligeros. Hay soluciones que suelen aplicarse en coches deportivos de altas prestaciones o en coches de competición, pero se aplican aquí al que podría ser un coche de producción en serie. Por ejemplo:
Los brazos de la suspensión delantera y del eje trasero son de aluminio.
Sistema de escape compacto, más corto y construido con materiales ligeros.
El sistema de frenado desarrollado por Continental pesa 14,5 kg menos que uno normal, entre otras cosas porque todas las funciones (freno, asistencia, ABS, ESP, etc) se agrupan en una sola caja, pero también al emplear discos de freno con núcleo de aluminio (y disco de acero) o tambores traseros de aluminio, salvo la zona de fricción, de acero.
Los cristales de vidrio son más delgados, y todos laminados (parabrisas y ventanillas de las puertas delanteras): con el proveedor Saint Gobain se ha desarrollado un parabrisas que tiene un espesor de tan solo 3 mm (cuando lo normal serían 4,5 mm). Los cristales traseros y la luna trasera son de plástico (policarbonato).
Los asientos desarrollados junto con el proveedor Faurecia son también más ligeros y delgados, utilizando materiales menos densos como el aluminio, magnesio o fibra de carbono.
Las piezas plásticas de los revestimientos pesan también menos: con plásticos de menor espesor, o utilizando un plástico que en el momento de inyectarlo en el molde se espuma quedando encerradas pequeñas burbujas de aire, para que la pieza resultante sea más liviana. Pero también hay otros elementos que pesan menos como los conductos de aire para la ventilación y climatización del habitáculo, fabricados en polipropileno expandido.
Mañana en la segunda parte os explicaremos cómo es su motorización híbrida enchufable, y su caja de cambios sin embrague, y también hablaremos de su interior digital y de nuestras primeras impresiones de conducción.
Continuará...