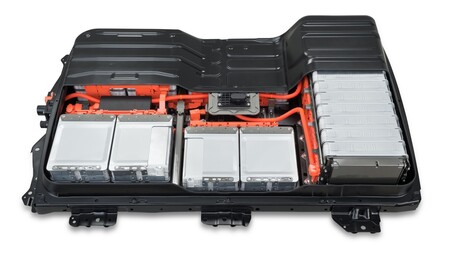
Uno de los mayores retos para la industria de la automoción y particularmente para la expansión sostenible de los coches eléctricos es la gestión de los materiales utilizados para fabricar sus baterías.
La utilización de tierras raras y su reciclaje son un escalón clave en la carrera por la electrificación, la descarbonización y la ruptura con la dependencia del petróleo. Ahora un instituto sueco ha detallado el proceso de reciclaje para recuperar el 100% de los materiales con los que se fabrican los electrodos.
Un proceso, de momento, a escala de laboratorio
Las baterías de los coches eléctricos son elementos altamente complejos, no sólo a nivel técnico, sino también por los materiales que se utilizan. Cobalto, níquel, litio y manganeso son productos escasos en la naturaleza y con procesos de extracción altamente contaminantes, por lo que averiguar cómo la industria puede recuperarlos es fundamental.
El instituto de investigación de metales SWERIM AB (Suecia) ha publicado un estudio en la Journal of Power Sources en el que pormenorizan a escala de laboratorio un procedimiento con el que reciclar las baterías con una eficacia del 100%, recuperando todos los metales de las celdas.
El proceso químico consiste en fundir los metales simultáneamente y aplicar posteriormente una reducción. El resultado sobre el papel es que las de una batería de iones de litio se puede obtener el cobalto, níquel y manganeso en aleación y el litio como polvo de la combustión (haluros de litio volátiles que se atrapan en la chimenea).
Para conseguir estos resultados, el SWERIM diseñó un procedimiento por el que el óxido de los metales de los electrodos (litio, níquel, manganeso y cobalto) pasan a convertirse en una aleación de los propios metales originales. Esto se logra añadiendo grafito y fluorida, e introduciendo la mezcla en un horno de argón a 1.550ºC para su combustión.
El resultado conseguido fue una aleación metálica con un 69,1% de cobalto, 14,4% de níquel y 5,8% de manganeso con el 100% de los metales introducidos en el horno y un nivel mínimo de escoria, mientras que el óxido de litio se recoge en forma de vapor de metal de litio al intentar escapar por la salida de gases.
Además el SWERIM apunta a una aleación resultante con un nivel mínimo de escoria gracias a que no se añaden otros productos químicos, minimizando la pérdida de materiales posterior debido al refinado necesario. También señalan que este proceso no es caro, ni en términos económicos ni ambientales, y no requiere una adaptación tecnológica. Basta con la infraestructura industrial existente.
Ahora el siguiente paso es que este procedimiento pueda dar el paso de la escala de laboratorio empleada por el instituto sueco a escala industrial. El SWERIM ha dado el primer paso, ahora le toca a la industria para comprobar la viabilidad en la práctica.
En Motorpasión | Drive-thru o comprar sin bajar del coche. Del banco que permitía hacer ingresos sobre ruedas al triunfo del McAuto y compañía